The Science Behind Laser Cleaning: How It Works and Why It’s Effective
- Rydex Laser
- Mar 25
- 2 min read
Laser Cleaning: A New Standard in Surface Preparation
Laser cleaning—also referred to as laser ablation—represents a significant advancement in surface treatment technology. By applying short, controlled pulses of high-energy light, laser systems can remove rust, paint, oxide, oil, and other contaminants with remarkable accuracy and minimal disruption to the substrate.
It’s a non-contact, chemical-free method that delivers results where conventional techniques like sandblasting, chemical stripping, or manual abrasion often fall short.
The Underlying Physics: Controlled Energy at Work
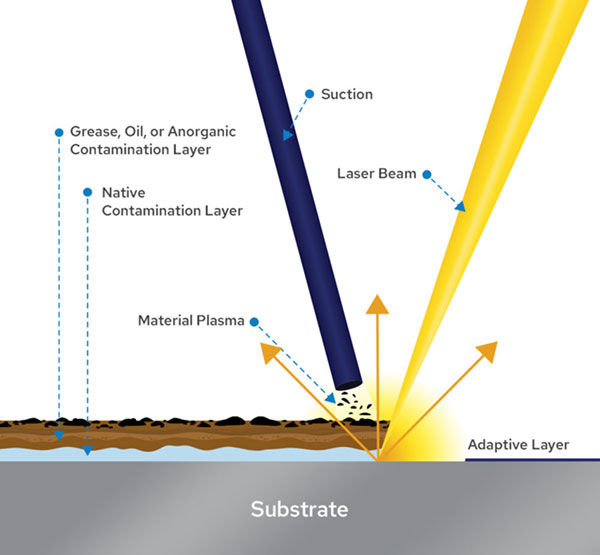
Laser ablation operates on a straightforward principle: differential absorption. Contaminants such as rust or paint absorb laser energy at different rates than the substrate beneath them. As the laser pulses strike the surface:
The contaminant layer rapidly heats, expands, and is ejected.
The base material, which reflects more of the laser’s wavelength, remains untouched and undamaged.
This high degree of selectivity makes laser cleaning particularly well-suited for sensitive or high-precision components — such as weld seams, machined parts, or surfaces where dimensional integrity is critical.
Key Advantages Over Traditional Methods
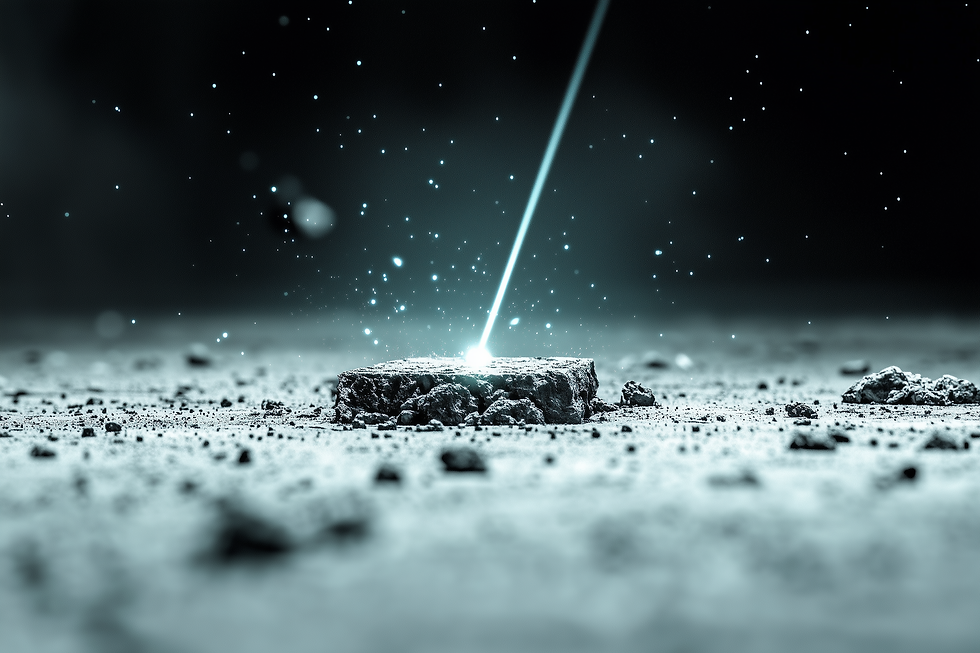
1. Micron-Level Precision
Laser systems can be calibrated to remove coatings as thin as a few microns, ensuring no collateral damage to adjacent surfaces or underlying material.
2. No Media, No Waste
The process produces no secondary waste streams — no spent media, no chemical runoff, no dust clouds. Material either vaporizes or is easily captured with standard extraction systems.
3. Broad Material Compatibility
Laser cleaning is effective on metals (including aluminum, stainless steel, copper, and titanium), ceramics, stone, and select polymers. It can remove a wide variety of contaminants without altering surface geometry or finish.
4. Repeatable, Controllable Results
With programmable settings and real-time feedback, laser cleaning ensures consistent outcomes across jobs — ideal for applications requiring validation, such as aerospace or medical manufacturing.
5. Improved Long-Term Performance
By preserving the surface condition and avoiding abrasive micro-damage, laser-treated components often show better resistance to future corrosion or wear.

Applied Use Case: Weld Prep in Aerospace Manufacturing
Consider an aerospace fabrication shop preparing titanium components for inspection. Traditional cleaning methods risk embedding foreign particles or altering the surface layer— issues that can lead to non-conformance. Laser cleaning, however, enables precise surface conditioning without introducing contaminants or compromising tolerances. It’s not just cleaner — it’s smarter engineering.
A Future-Focused Approach to Industrial Cleaning
As regulatory environments tighten and industries push for cleaner, safer, and more efficient processes, laser cleaning is emerging as a go-to solution. It's being integrated into workflows not only for its environmental and safety benefits, but also for the repeatable, high-precision results it offers.
As laser cleaning technology evolves, its role across sectors will continue to expand—from heritage conservation to high-performance manufacturing. It’s not a supplement to traditional methods; it’s a step forward.
To learn more about integrating laser cleaning into your operations, get in touch with our team!
Comments